Compact solution for creep-feed grinding
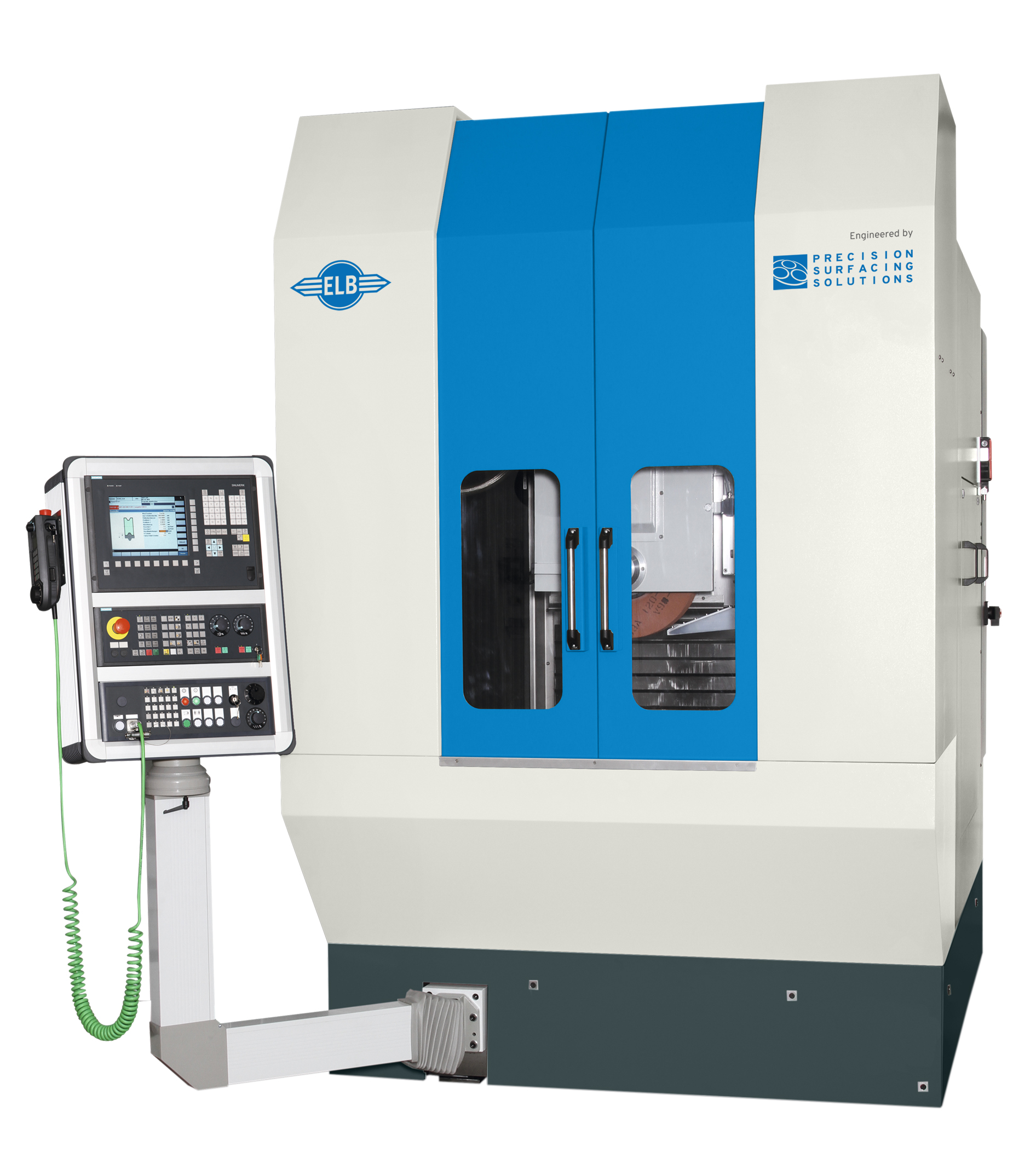
The microCut model was specifically designed to meet the requirements of profile and creep-feed grinding applications. The modular column design offers a small footprint which can be easily configured into economical production cells frequently used in the turbine manufacturing industry.
This machine is available in compact standard sizes but special designs with spindle power up to 52 kW are also available.
The integration into production lines is achieved through automatic material handling and tool changers. A common solution to reduce non-productive time is to equip the microCut with an index table to allow loading and unloading during the machining cycle.
For high-precision applications, dressing of the grinding wheel can be done on the table with a roll dressing unit or via interpolation of feed and cross axes. For high-production grinding, head mounted roll dressing units for intermittent or continuous use are available. For complex grinding tasks, dual head mounted dressing units and tool changers are being used. The microCut is frequently used with Corundum, CBN and diamond grinding wheels. A trunnion table can be mounted on the machine table to allow the processing of multiple sides of a workpiece. With the Siemens SINUMERIK ONE control the microCut can grind complex shapes by interpolating multiple axes. Proven ELB programming templates are available for most grinding applications. We have application engineers and programmers on staff for every grinding task.
Design Characteristics
- Compact modular building block design
- Easy rigging and placement with attached electrical cabinet
- Preloaded linear guideways for all axes
- Use of vertical and horizontal indexing devices
- Oversized spindle and grinding wheels for large material removal capacity
- Grinding wheel attachment via cone or HSK
- Optional grinding wheel changer
- Optional automatic loading and unloading of workpieces
Benefit Overview
- Compact machine design
- High material removal rate
- High long-term precision
- Ideal for cell layouts
- Optional index table for loading/unloading while grinding
- Optional automatic tool changer
microCut | 250 | 320 | 320 DS | 520 |
Grinding Width (mm) | 275 | 400 | 220 | 600 |
Grinding Length (mm) | 500 | 700 | 900 | 700 |
Distance Spindle Center to Table (mm) | 400/600 | 700 | - | 400/600 |
Spindle motor (kW) | 22/37/52 | 37/52 | 37/52 | 37/52 |
Spindle cone (mm) | 75 | 75/90 | 75/90 | 90/125, HSK 100/125 |
Wheel size (mm) | 400 x 100 x 127 | 500 x 100 x 203.2 | 500 x 100 x 203.2 | 500 x 160 x 203.2 |
All values are approximated and may change depending on selected options. All information is subject to change.